ASUS AIoT Membangun Solusi Manufaktur Pintar Terbaru untuk Mempromosikan Peningkatan Industri
4 min read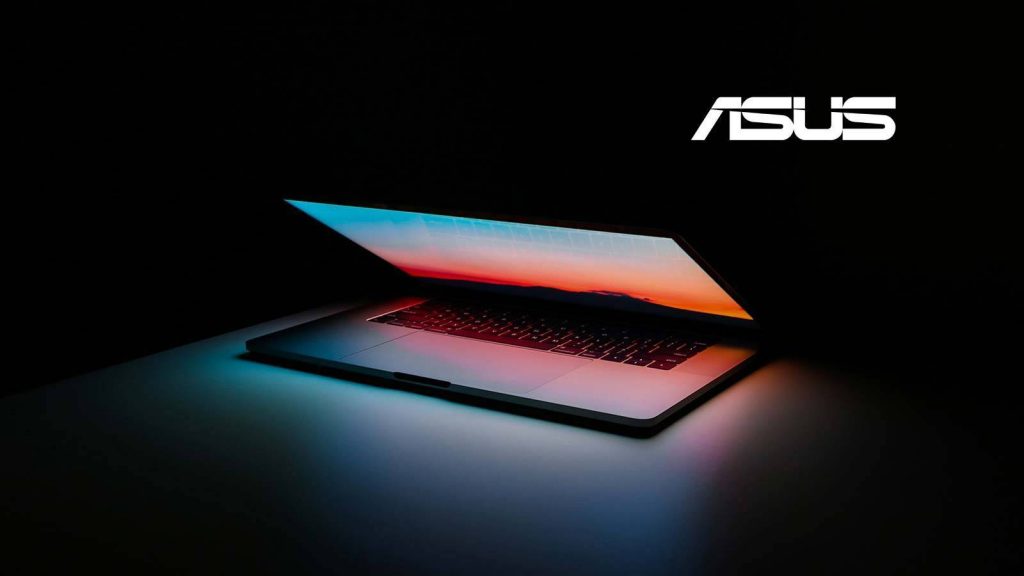
JAMBIDAILY TEKNOLOGI – Dengan munculnya era AIoT, ASUS telah merangkul teknologi dan metode baru untuk mengembangkan kemampuan manufaktur yang maju. Pada akhir tahun 2019, ASUS memperluas unit bisnis AIoT untuk dapat mengembangkan lebih banyak solusi untuk industri dan dalam prosesnya, menamai dengan AIoT Business Group (AIoT BG). Setelah mempertimbangkan dan merencanakan sekitar tiga aspek utama dari manufaktur yang sukses – desain daya, kemampuan teknis dan profitabilitas berkelanjutan – ASUS mengubah operasi untuk mencapai fleksibilitas, kecepatan, produktivitas dan kualitas yang diperlukan untuk peningkatan pasokan Industri 4.0.
Mendeteksi cacat secara manual adalah kesulitan utama dan penyebab ketidakefisienan dalam proses pembuatan. Dengan berinvestasi pada solusi pabrikan pintar yang memanfaatkan teknologi AI untuk memproduksi periferal logam, kipas, papan sirkuit cetak dan komponen komputer lainnya serta untuk perakitan sistem, ASUS dapat menghilangkan hambatan efisiensi dan mengurangi kerugian akibat kesalahan penilaian cacat pabrikasi oleh karyawan pabrik. Kedepannya, ASUS akan terus menggunakan kecerdasan buatan dan big data untuk secara statistic mengklasifikasikan berbagai jenis cacat kualitas, menentukan penyebabnya dan meningkatkan proses pada sumber cacat untuk lebih meningkatkan dan mendorong batas-batas kualitas manufaktur.
“ASUS saat ini memiliki ratusan pemasok, dan setiap kali kami dapat meningkatkan proses pemeriksaan kualitas, pemasok akan menerima dan bersedia melakukan perubahan,” ujar Jackie Hsu, Wakil Presiden Senior, Co-Head of Open Platform BG & AIoT Business Group mengatakan. “Ini adalah situasi paling menguntungkan bagi ASUS dan seluruh industri yang selalu mementingkan kualitas produk.”
Sistem Inspeksi Visual AI
Dalam industri manufaktur, adalah merupakan hal umum untuk mengganti inspeksi visual manual dengan inspeksi optik otomatis (AOI). Namun, inspeksi optik tidak efisien untuk produsen komponen logam mekanis. Inspeksi visual manual seringkali membutuhkan tampilan permukaan produk dari berbagai sudut untuk melihat cacat akibat pantulan cahaya. Sangat penting untuk memahami karakteristik permukaan optik dan komponen untuk mendapatkan data cacat yang lengkap dan benar.
Inspeksi optik adalah salah satu teknologi inti dari AIoT Business Group, yang menggunakan pembelajaran mesin, pembelajaran mendalam dan teknologi jaringan saraf tiruan untuk melatih model deteksi AI dengan benar. “Keakuratan inspeksi optic otomatis secara umum adalah sekitar 80-90%, yang berarti bahwa lebih dari 10% kesalahan penilaian cacat dapat terjadi, dan akurasi inspeksi visual manual adalah sekitar 90%,” kata Albert Chang, Corporate Vice President, Co-Head of AIoT Business Group. “Saat ini, ASUS telah memungkinkan AI untuk meningkatkan akurasinya sangat tinggi hingga 98% setelah proses pembelajaran.”
Sistem deteksi gelombang AI
Kipas adalah bagian penting dari banyak komputer dan elektronik konsumen, komponen pendingin dan membantu memperpanjang usia produk. Untuk memastikan kualitas kipas, pabrikan mengandalkan inspektur yang mampu mendeteksi masalah dengan kipas hanya dengan mendengarkannya. Melatih personel yang sangat terampil untuk posisi penting ini memakan waktu tiga hingga enam bulan, dan pengawas kadang-kadang akan mengalami kelelahan telinga jangka pendek atau jangka panjang, dan faktor pekerjaan lainnya yang berdampak negatif terhadap kesehatan pekerja dan mengurangi tingkat deteksi masalah.
Untuk mengatasi masalah yang sulit ini, ASUS memperkenalkan Sistem Ciri Khas Gelombang AI ( AI Wave Signature System), yang menganalisa suara kipas yang beroperasi dengan benar dan menggunakannya untuk mengembangkan ciri khas suara. Ciri khas suara ini kemudian digunakan untuk melatih model AI agar dapat mengidentifikasikan dengan cepat kipas berkualitas tinggi. AI Wave Signature System dapat dikombinasikan dengan pengujian arus listrik, tegangan, getaran dan karakteristik produk lainnya selama inspeksi untuk memastikan kualitas produk secara keseluruhan. Selain itu, sistem dapat diterapkan untuk memantau peralatan produksi secara real time untuk menghindari waktu henti pabrik. Sebagai contoh, dengan memonitor motor peralatan di pabrik menggunakan AI Wave Signature System, operator akan diberitahu segera jika motor mulai berperilaku tidak normal. Motor kemudian dapat diperbaiki sebelum gagal sepenuhnya, menghindari penghentian produksi secara tiba-tiba dan kerugian yang menyertainya.
Reproduksibilitas sebagai model bisnis ASUS AIoT
Tahun ini, Grup Bisnis ASUS AIoT telah menetapkan target agresif dengan pemasok kipas dan komponen mekanis serta diperkirakan akan mengakuisisi 30 proyek inspeksi pintar. “Tujuan asli dan prioritas utama grup bisnis adalah untuk mempromosikan peningkatan bersama di industri dan membantu peningkatan rantai pasokan untuk menghadapi persaingan internasional dan terus mengumpulkan pengalaman,” ujar Jackie Hsu, Senior Vice President dan Co-Head of the Open Platform serta AIoT business groups.
Mengomentari pengenalan manufaktur pintar dan solusi deteksi AI oleh pabrik-pabrik besar, Albert Chang, Corporate Vice President dan Co-Head AIoT business group mengatakan, “Di masa lalu, algoritma dan model AI sangat disesuaikan,meningkatkan potensi solusi deteksi AI. Reproduksibilitas adalah tujuan dari tahap berikutnya, memungkinkan popularisasi cepat dan adopsi bersama dengan skalabilitas. Akhirnya, visi akhir dari grup bisnis ASUS AIoT adalah untuk fokus pada ‘analisis kualitas penuh‘.”
Target ASUS AIoT untuk tiga hingga lima tahun kedepan adalah analisis data. Dengan menyelidiki penyebab cacat, membantu rantai pasokan untuk menemukan solusi mendasar untuk hasil tinggi, membuat formula untuk sukses dan mengumpulkan nilai jangka panjang, analisis data akan menjadi pilar penting dari merek ASUS.